Advanced Rail Track Inspection Technologies for Enhanced Railway Safety
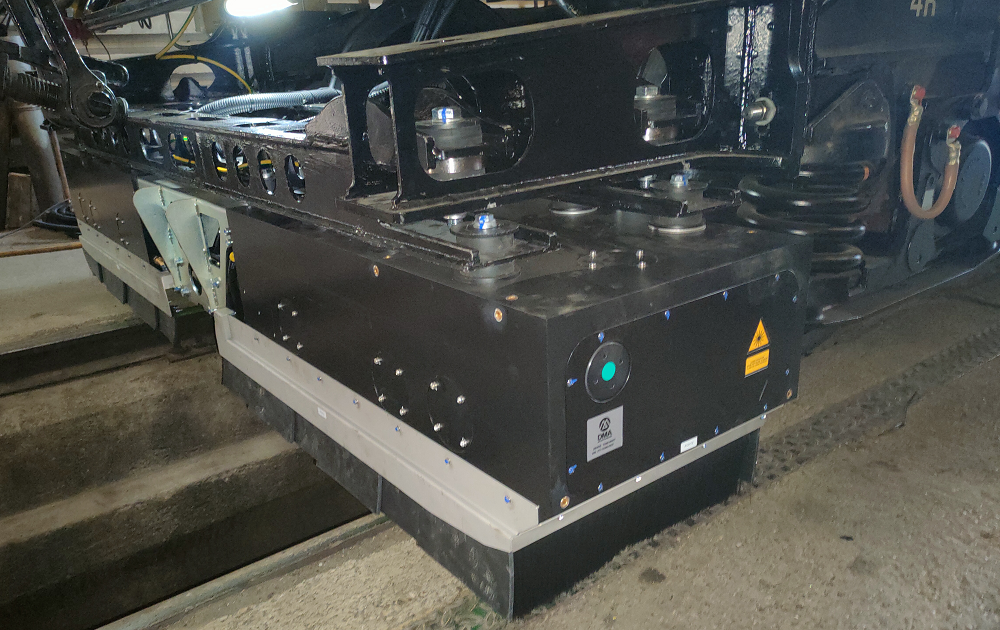
Innovative Rail Inspection Technology: Ensuring Safety and Efficiency
Regular and precise track inspections are essential for ensuring railway safety, complying with regulatory standards, and optimizing maintenance costs. Advanced technologies like DMA’s Track Component Video Inspection System provide the tools needed to perform these inspections efficiently and accurately. Don’t compromise on safety and invest in the best inspection technologies available. Contact DMA today to learn how our cutting-edge solutions can help you maintain a safe and reliable railway infrastructure.
In the realm of railway safety, track inspection is a cornerstone activity that ensures the reliability and integrity of rail infrastructure. As rail networks expand and the demand for efficiency increases, the methods and technologies used for track inspection have evolved significantly. Traditional visual inspection, while still useful, has been supplemented and in some cases replaced by advanced automated track inspection systems that offer unparalleled precision and efficiency.
The visual inspection methods involve inspectors physically examining the track on foot or from a slow-moving vehicle. This approach relies heavily on the expertise and experience of the inspectors to identify potential defects and anomalies. Key parameters checked during visual inspections include rail alignment, surface wear, ballast condition, and the state of rail fasteners and joints. Despite its importance, this method has limitations, particularly in terms of coverage speed, potential human error, and the ability to operate under various weather conditions and lighting.
To address the limitations of manual inspections, the railway industry has increasingly turned to automated track inspection technologies. One such innovation is DMA’s Track Component Video Inspection System (TCVIS). This system utilizes high-speed linear cameras and LED illuminators to capture continuous images of the track and its components. The TCVIS system can operate at speeds of up to 90 km/h and higher, ensuring that inspections do not disrupt regular train operations. The captured images are analyzed using advanced algorithms, including deep neural networks and morphological algorithms, to detect a wide range of defects such as cracks, gaps, and wear.
The automated inspection systems like our Track Component Video Inspection System provide a higher level of detail and accuracy compared to manual inspections, significantly reduce the risk of human error, and enable continuous monitoring of track conditions. Additionally, these systems can operate in a variety of environmental conditions, providing reliable data regardless of lighting or weather.
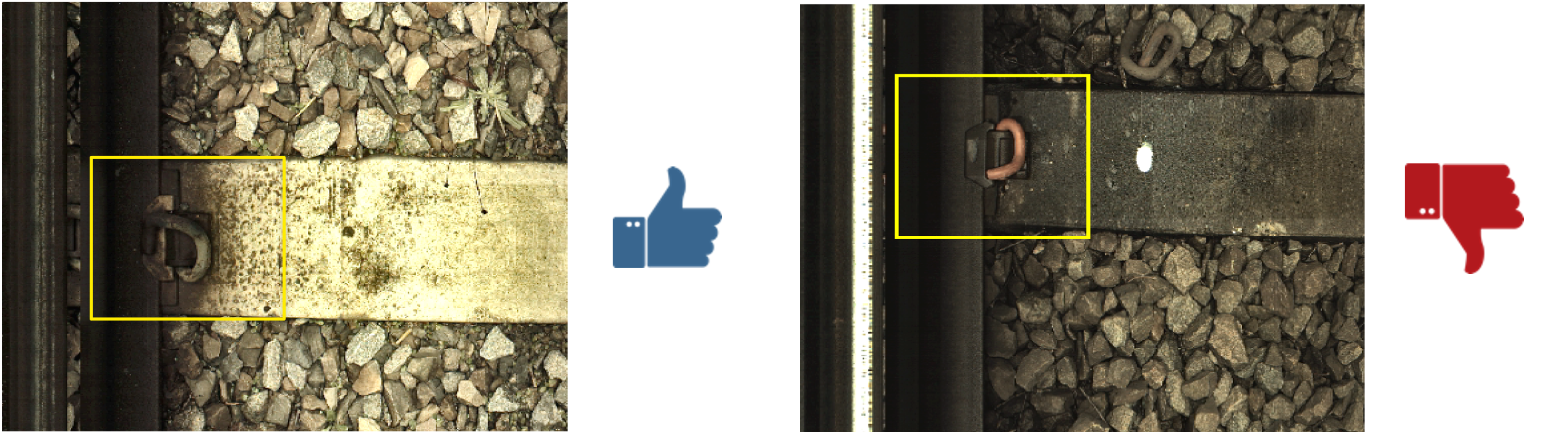
Modern rail inspection does not rely on a single technology but often integrates multiple systems to provide a comprehensive assessment. For example, DMA’s Track Component Video Inspection System can be combined with track geometry measurements with inertial measurement units (Track Geometry Measurement System TGMS), enhancing the detection capabilities and providing a holistic view of track status. This integration allows for the measurement of critical parameters such as gauge, alignment, cross level, longitudinal level, and twist, which are essential for maintaining track stability and safety.
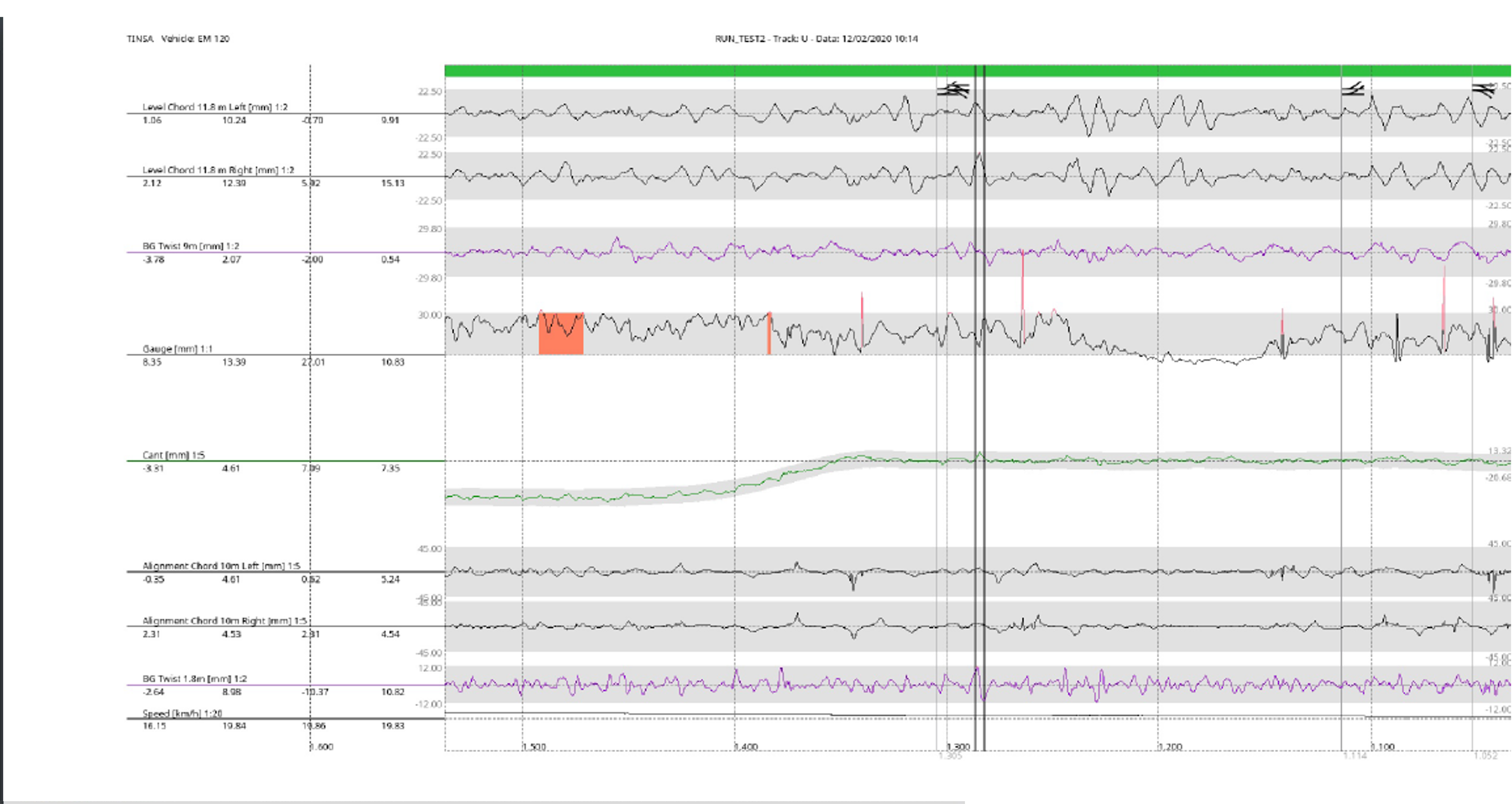
The vast amount of data generated by automated inspection systems requires robust data management and analysis tools. Systems like DMA’s utilize network-attached storage devices for centralized data management, ensuring that all measurement data is stored in a single location for easy access and analysis. Advanced software tools then process this data, identifying trends and predicting potential failures before they occur. This predictive maintenance approach not only enhances safety but also reduces maintenance costs by addressing issues before they become critical.
Crucial Measurements in Rail Track Monitoring
Rail track inspection encompasses a variety of measurements that are critical for maintaining the integrity and safety of the railway infrastructure. Understanding what can be measured and why these measurements are essential is key to appreciating the importance of regular and precise track inspections.
Track geometry is one of the fundamental aspects measured during rail track inspections. It includes many parameters, as we said before, and these measurements ensure that the tracks are correctly positioned and aligned. For instance, the gauge is the distance between the inner sides of the two rails, and any deviation from the nominal gauge can lead to derailments. Alignment refers to the horizontal positioning of the track, while the cross level measures the vertical difference between the two rails and the twist is the variation in cross level over a short distance, which is important for the risk of derailments.
The condition of the rail itself is another crucial inspection. Over time, rails can develop wear patterns that, if left unchecked, can lead to failures. Rail profile measurement involves assessing the rail’s cross-sectional shape to detect wear and deformation. This measurement is vital for allowing a correct maintenance to permit smooth and safe train operations.
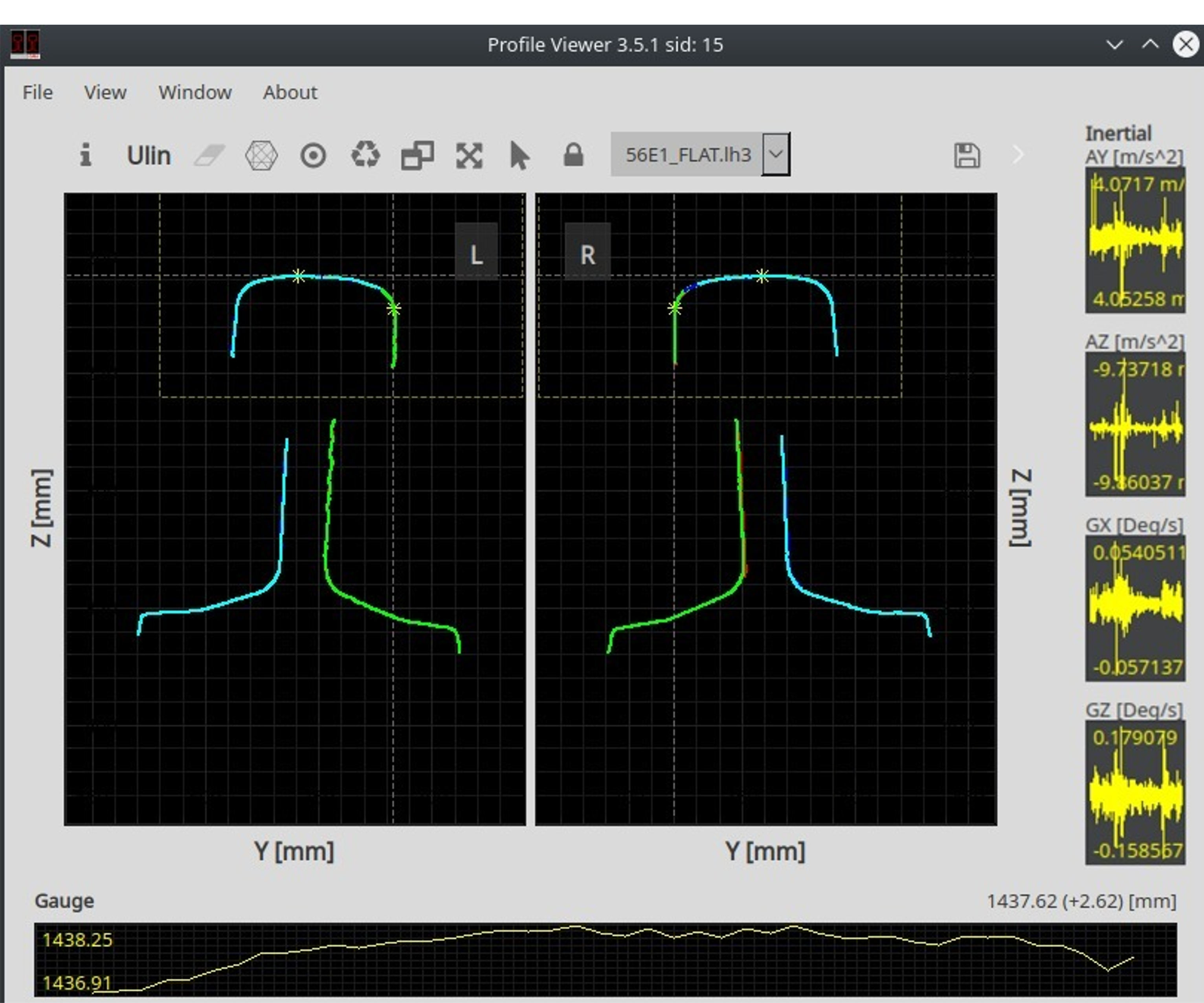
Knowing the critical role played by rail wear measurement, we designed our Rail Profile Measurement System (RPMS) for using high-resolution cameras that capture detailed images of the rail profile, allowing for accurate detection of wear and other defects.
Fasteners and joints hold the rail in place and connect different sections of the track. The condition of these components is obviously crucial for track integrity. Loose or broken fasteners and joints can lead to track misalignment and increased risk of derailments. Our Track Component Video Inspection System inspects these components using advanced imaging and analysis techniques to detect issues such as loose clips, missing bolts, and defective clamps.
The Importance of Rail Track Inspection for Safety
Railway safety is a paramount concern for operators, regulators, and passengers. Ensuring that rail infrastructure is in optimal condition is crucial for preventing accidents and maintaining efficient operations. Regular and thorough track inspections play a vital role in achieving these goals.
One of the primary reasons for regular track inspections is to prevent accidents. Rail infrastructure is subjected to constant stress from heavy loads and environmental factors, which can lead to wear and tear over time. Defects such as cracks, misalignments, and wear can compromise the integrity of the tracks and increase the risk of derailments. Early detection of issues ensures that they are addressed before they can cause accidents, significantly enhancing the safety of rail operations.
Railway operators are required to comply with stringent safety standards set by regulatory bodies. These standards, such as those outlined by the Federal Railroad Administration in the United States, mandate regular track inspections and specify the parameters that must be monitored. Failing to comply with these standards can result in severe penalties and increased risk of accidents. Automated inspection technologies help operators meet these regulatory requirements more efficiently and accurately. By using systems like the Track Component Video Inspection System, operators can ensure that their inspections are thorough and comply with all relevant safety standards, thereby avoiding penalties and enhancing overall safety.
Regular track inspections are not only crucial for safety but also for cost-effective maintenance. Identifying defects early allows for smaller, less expensive repairs rather than more extensive and costly overhauls. Automated inspection systems provide continuous monitoring and detailed data, which can be used to predict when and where maintenance is needed. Predictive maintenance optimizes schedules and save resources, reducing downtime and operational costs.