Effective Turnout Maintenance with DMA’s TCMS: Ensuring Railway Safety
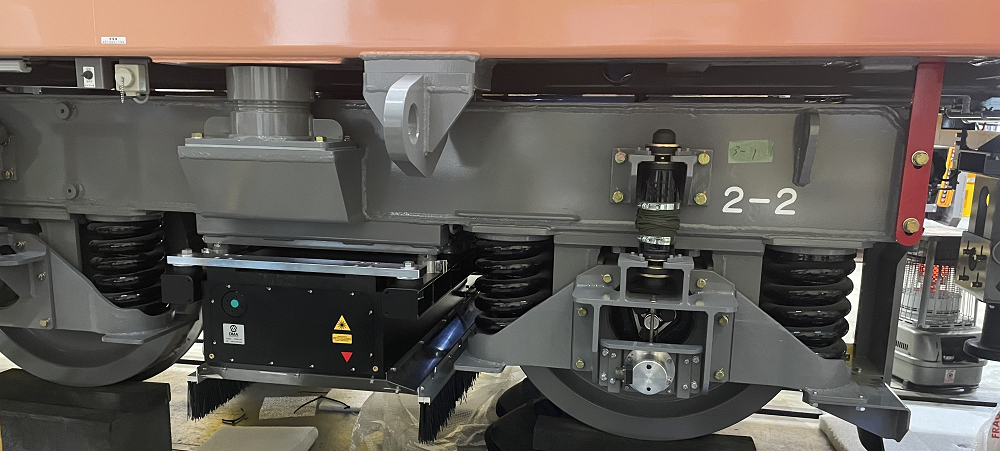
Railway Turnout Inspection: Essential Parameters for Safety
Railway turnouts, also known as switches, play a pivotal role in railway operations by enabling trains to transition from one track to another. For companies engaged in railway infrastructure management, mastering the key parameters of turnout inspection is essential for maintaining safety and efficiency and our Turnout and Crossing Measuring System (TCMS) can help to keep a close eye on these crucial data.
We in DMA have highlighted some key measurement parameters for turnout inspection and maintenance:
- Free Wheel Passage (Fwps): This parameter measures the space available for the wheel to pass through the switch and crossing areas. It ensures that there is adequate clearance to prevent derailments and maintain smooth operations. The Free Wheel Passage is crucial in the switch panel, closure panel, and crossing panel.
- Nose Protection (Npof): This involves assessing the protection provided at the nose of the crossing, ensuring it can withstand the impact and wear caused by passing trains. Proper nose protection helps to maintain the integrity of the crossing and prevents damage that could lead to service interruptions.
- Flangeway Depth (Hfw): The depth of the flangeway is measured to ensure that the flanges of the train wheels can pass through without obstruction. This is critical for maintaining the correct alignment and preventing derailments, especially at higher speeds.
- Gauge and Alignment: Accurate measurement of the track gauge, both loaded and unloaded, is essential. The gauge under load reflects the real geometry of the turnout when a train passes over it, which is critical for identifying any deformations or misalignments that could affect safety. Additionally, alignment and longitudinal level measurements are performed to detect any deviations from the optimal track position.
- Switch Wear: The wear on the switch rails, including the tongue and stock rails, has to be closely monitored. Over time, these components can wear down, leading to gaps that can affect the smooth transition of trains from one track to another. Regular inspection helps in identifying wear patterns and planning maintenance activities to replace or repair worn parts.
- Crossing Wear: Similar to switch wear, the wear on the crossing or frog is inspected. This includes the wear on the wing rails, the Vee, and any movable parts of the crossing. Ensuring these components are in good condition is vital for maintaining the continuity and safety of the track.
By focusing on these parameters, railway companies can ensure that their turnouts remain in optimal condition, reducing the risk of accidents and service disruptions. Regular inspections and maintenance activities based on these measurements help in identifying potential issues before they become critical, ensuring the safety and reliability of railway operations.
Turnout inspections are not merely a regulatory requirement but a fundamental aspect of railway safety management. Regular and thorough inspections using advanced systems like DMA’s TCMS allow for precise measurement and early detection of potential issues. This proactive approach to maintenance ensures that any irregularities are addressed promptly, thus preventing accidents and enhancing the overall efficiency of the railway network.
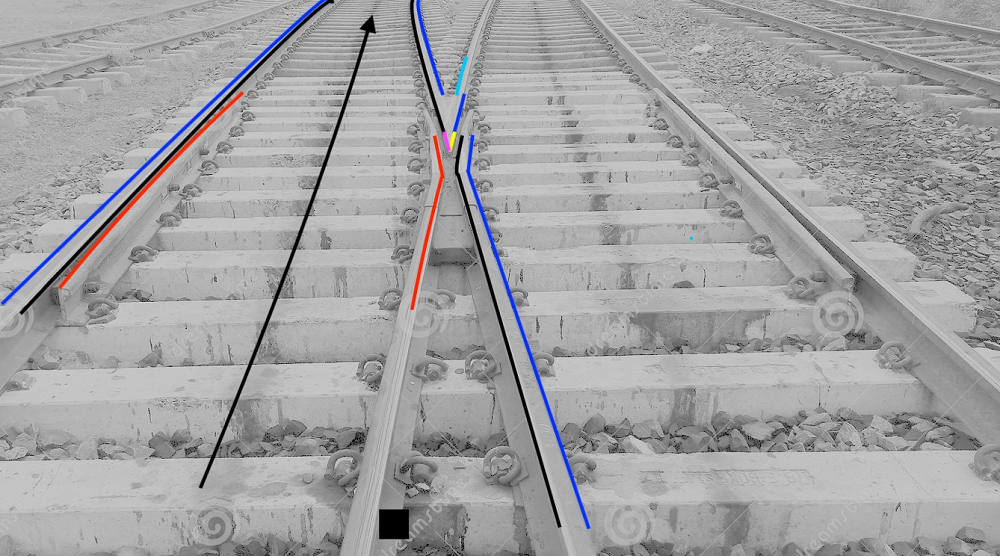
Turnout Maintenance: Improving Worker Safety with Automated Systems
One of the significant advantages of DMA’s TCMS (Turnout & Crossing Measurement System) is the reduction in the need for trackside personnel during inspections. By automating the turnout maintenance process, the TCMS enhances safety for workers and efficiency for railway operations.
The traditional method of inspecting turnouts involves manual inspections by personnel working directly on the tracks. This approach not only exposes workers to the risk of accidents but also requires significant time and resources. With the automation provided by TCMS, inspections can be conducted without the need for personnel to be physically present on the tracks.
DMA automated systems perform detailed measurements and inspections using advanced sensors and cameras, which can detect wear, misalignments, and other issues with high precision. This eliminates the need for manual measurements and observations, allowing workers to focus on analyzing the data and planning maintenance activities from a safe location.
Using our TCMS leads not only to enhance workers safety, but also to three additional benefits:
- Higher Inspection Accuracy: The TCMS uses precise optical measurement technology to inspect turnouts. This ensures that even minor issues are detected early, preventing potential failures that could lead to accidents or service disruptions.
- Efficient Data Collection and Analysis: The system collects vast amounts of data in a single pass, which is then analyzed using advanced software. This allows for a comprehensive understanding of the condition of the turnout and supports proactive maintenance planning.
- Consistency and Repeatability: Automated inspections provide consistent results that are not subject to human error. This repeatability is crucial for maintaining high standards of safety and reliability in railway operations.
With the detailed and accurate data provided by the TCMS, railway companies can shift from a reactive to a proactive maintenance strategy. Instead of responding to failures and disruptions, maintenance teams can use the data to identify potential issues before they become critical. This approach not only improves safety but also dramatically reduces maintenance costs and minimizes downtime.
Another key benefit of using the TCMS is its minimal impact on commercial rail traffic. Traditional manual inspections often require track possession, which can disrupt normal train operations and lead to delays. In contrast, the TCMS can perform inspections without requiring significant track occupation. The system is designed to operate alongside regular train services, ensuring that inspections are conducted with almost zero impact on revenue service.
This capability is particularly valuable for busy railway networks where maintaining uninterrupted service is critical. By integrating the TCMS into their maintenance programs, railway companies can ensure continuous monitoring and inspection of their infrastructure without compromising on operational efficiency.
Turnout and Crossing: Efficient Inspections with Minimal Traffic Impact
Maintaining turnouts is crucial for the safety and efficiency of railway transport. As we said before, DMA’s TCMS allows for comprehensive turnout inspections without disrupting commercial rail traffic. This system’s ability to operate with minimal impact on train schedules ensures that maintenance activities do not interfere with daily operations, providing seamless and continuous railway service.
A well-maintained turnout reduces the risk of derailments and accidents, which can have severe consequences for both passengers and cargo. Regular inspection and maintenance of turnouts help in identifying wear and tear, misalignments, and other potential issues that could compromise safety. By leveraging the advanced capabilities of DMA’s TCMS, railway companies can ensure that their turnouts are in optimal condition, thereby enhancing the overall safety of the railway network.
In effect, our Turnout & Crossing Measurement System have some crucial features that allows a high quality maintenance management:
- Non-Intrusive Inspections: The TCMS uses advanced optical measurement technologies that do not require physical contact with the track. This allows inspections to be carried out without interfering with train movements.
- High-Speed Data Collection: The system can inspect turnouts and crossovers at speeds of up to 30 km/h for detailed measurements and up to 200 km/h for general track geometry. This high-speed capability ensures that inspections are quick and efficient, minimizing the time required on the tracks.
Real-Time Data Processing: The TCMS processes data in real-time, providing immediate insights into the condition of the turnouts. This enables maintenance teams to make prompt decisions and schedule necessary interventions without delay.
- Data Processing: The TCMS processes turnout data in post-processing, providing insights into the condition of the turnouts. This enables maintenance teams to make prompt decisions and schedule necessary interventions without delay.
- Scheduled Inspections: The system can be programmed to perform inspections at scheduled intervals, ensuring that maintenance activities are planned and executed systematically.
We are proud that DMA’s TCMS represents a significant advancement in turnout maintenance by enabling efficient, non-intrusive inspections that do not interfere with regular train operations. Furthermore, the integration of TCMS into maintenance programs allows for proactive management of railway infrastructure, minimizing risks, and optimizing performance.
In conclusion, the use of DMA’s TCMS for turnout and crossover maintenance offers railway companies substantial benefits, including enhanced safety, cost-effective maintenance, and minimal impact on commercial rail traffic. This innovative system empowers railway companies to maintain their infrastructure more effectively, ensuring continuous and reliable service for all users.